Success Story:
Automated energy management at Carl Eichhorn
Carl Eichhorn KG Wellpappenwerke is now recording energy data in an automated way thanks to post-networking: energy measurement data is recorded via IIoT boxes and transferred to the openpack digital platform. This gives the company control over its current energy and resource consumption at a glance, recognizes potential savings and can react more quickly to deviations.
Carl Eichhorn got talking to the team behind openpack, the digital platform for the corrugated board industry. They realized that they were looking for a simple solution for the energy and resource management of the machines. This is because providing evidence for certifications such as ISO 50001 is time-consuming: In practice, the data collection and evaluation for this is extremely cumbersome. The corrugated cardboard manufacturer wanted a solution that would make it easier to break down the machines’ energy consumption and identify potential savings.
Importance of digitalization for Carl Eichhorn “massive”
The openpack team advised digital data capture with the openpack platform. In doing so, openpack opened the doors of the well-known family business. Carl Eichhorn considers the impact of advancing digitalization on its business to be “massive”. Managing Director Martin Keirath says: “In order to be able to offer a mass product such as corrugated board efficiently and cost-effectively, all areas of corrugated board production must be more automated than before.” He firmly believes that the next five years will see pioneering digital simplifications for the corrugated board industry.
Professionalizing energy monitoring by means of retrofitting and networking
The task was to record energy data such as voltage and current curves, active power and much more as simply as possible and transmit it to openpack. The data is collated in the platform. In the long term, the aim is to create a database that can be used to recognise anomalies and deviations at an early stage. ‘We were impressed by the open platform and the team,’ says Martin Keirath, explaining the reasons why the company opted for openpack. ‘The combination of openpack and the connected systems results in a well-rounded overall package for more speed.’ The proposal was to start by retrofitting the FFG 8.20 inline machine. A concept for the planned retrofitting was developed together. Openpack brought mCloud Systems on board as a reliable partner.
The company specialises in sensor communication and IoT scenarios with robust communication connections and simple integration options. They set to work together. The keyword was retrofitting – modernising and retrofitting existing systems and machines. The IIoT boxes and the current clamps were fitted to the machine in a short space of time and with little installation effort. The boxes can be mounted flexibly and transmit measured data wirelessly to openpack. The measurement is galvanically isolated, which means that there is no interference with the machine and the risk of a standstill due to the measuring equipment is avoided.
Improved efficiency and ease of use
The data from the FFG 8.20 machine is now automatically transferred to the connected platform. The result: greater efficiency and a precise overview of energy requirements and costs. It is possible to see at a glance where potential savings lie dormant – previously unthinkable. Managing Director Martin Keirath is satisfied: ‘I like the simple structure of the platform, which is easy for every user to operate. And we can quickly access operating instructions, machine data, production information or machine repair times, for example.’ The solution was also implemented quickly. The way is clear for further joint projects.
‘The openpack team and we will inspire each other and develop more exciting ideas,’ says Martin Keirath.
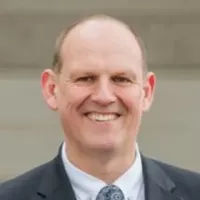
‘The speed at which the measures were implemented was impressive. I generally found the team behind openpack to be fast, solution-orientated and effective.’